Parts List
: |
Rock City -
Set of 4
beadlocks with anti-coning rings |
|
|
INTRODUCTION: Through lots of work and money I had
ended up with a crawl ratio around 75:1. The problem was that even
at 12 psi I would spin out on bigger rocks. I had to hit everything
in second (around 32:1). Any lower on the tire pressure and I’d be
rolling tires off the rims all the time. The answer: Beadlocks.
I started looking at complete rims but
they were a little pricey and would basically be the same as a kit
without the work. So I decided on a kit, which is added to your
existing steel wheels. I looked at several kits.
I ordered them from Rock City (Rob) (http://www.rockcityfab.com/
).
Basic rings for four wheels without
hardware is $220. Add hardware $245. Fancier outer rings and it goes
to $295. |
|
These are
the inner rings. All the rings come bolted together |
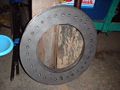 |
Here are the outers. I
got a little ahead of myself and painted them without getting the
raw look picture. This has been the downfall of several projects I
meant to write up. |
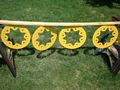 |
Here’s a close up. I sprung the extra
$12 a wheel to get the pimp-daddy specials. These are not only going
to help off road, but they look cool too. I painted these with
Rustoleum bare metal primer and then some gloss yellow. I traced
around these on some cardboard and made a couple templates so I can
touch these up once they are mounted without getting yellow on my
tires. |
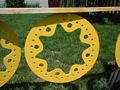 |
This is
the bolts & anti-coning rings. He sends these USPS because it’s much
cheaper. This is slower getting to you than the rings so relax.
Basically, anything that will fit in this box is the same price
regardless of weight. |
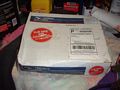 |
Here is
what’s in the box: All the bolts, washers, nylock nuts,
instructions, and the anti-coning rings. The anti-coning rings are
rolled pieces of steel that has to be tacked to the outer ring
according to the instructions. I will stray from this a little but
more on that later. |
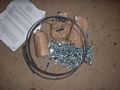 |
This is
what I had to work with. American Racing wagon wheels, 15 x 8 with 3
½ back spacing, 5 on 5.5 bolt pattern. Tires are 33 x 12.5-15
ProComp M/Ts. |
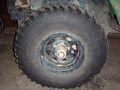 |
Closer view. Notice the valve stem
location. This will have to move. |
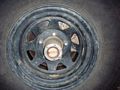 |
Here we
are, all 4 wheels in the trunk of my car heading to the welder at
work and my skilled friend. A note here: I can weld OK. I have a
stick welder and keep my Jeep together through various degrees of
damage. These welds need to be air tight, smooth, and small as
possible if I ever hope to balance this when I’m done. I have ground
the paint off all concerned areas and cleaned everything up. |
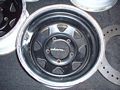 |
A close up
of the valve stem area: This points straight at the inner bead and
will be a pain to get to even with an angled valve stem. I will weld
it up and move it. |
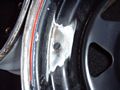 |
A mock up:
You can really see how the valve stem won’t work out.
I can’t get pictures of the welding
steps. Work has a strict camera policy. Basically, we will follow
the instructions. The valve stem holes will be welded up first
because the ring will make it harder if it’s in the way. We put a
piece of brass on the backside to make it easier to fill the hole.
Next, place the ring inside the wheel and center it. Tack it in
eight spots. Then weld in between the spots. We welded four
increments on opposite sides to keep warping to a minimum. Then
moved to the next wheel. Once we had all of them to this level we
went back finished each wheel.
|
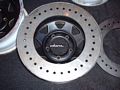 |
Well, I
got ahead again. This is primed after welding. The anti-coning ring
is a piece of 1/8” x ½” hot roll steel rolled into a circle (could
be easily made and added to the cheap kit). The instructions wanted
it welded on the outer ring but I can’t see why it makes a
difference. I got sixteen 10mm socket head bolts and stuck them in
every other hole. They are slightly larger than 3/8” (like .390) and
the head is a little bigger in diameter. Then pushed the ring out to
the bolt heads and tacked it good. You can use a vise grip to hold
it to the bolts. Repeat all the way around. The anti-coning ring is
longer than it needs to be so you’ll have to trim it. I used a 3”air
cut-off tool. Basically work from the middle of the ring out to the
ends. When you start getting close to the end make the cut. I jacked
the anti-coning ring up on a bolt or something to get it off the rim
some so I wouldn’t nick the inner ring on cut through. I then welded
the ends together. I will caulk all this on both sides once it’s
assembled to keep the water/mud out. |
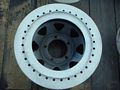 |
This is a
close up of the anti-coning ring and the welds. |
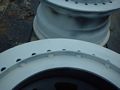 |
I ground
the weld flat at the rim. There is a small gap between the rim and
the ring prior to welding. This is where you want your wire pointed
when you weld. Then, when it is ground flat you still have a good
deep weld. |
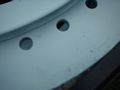 |
These two show the welded up hole and
the new location. I put it in line with the old hole figuring the
little blob of weld weigh would be offset by the new hole. The hole
is 29/64”. Drill it out with a smaller drill (like 13/32”) and
finish it with the 29/64”. |
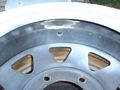 |
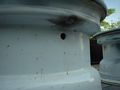 |
Once the
paint dries it will be time for the valve stem. |
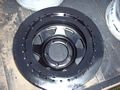 |
I picked
up the standard 1 ¼” long .453 dia. Vickers valve stems at the auto
parts store. For the tire mounting stuff I make up a little soapy
water solution to make the tires slide on better. It’s also useful
for leak checking. Lube the valve stem up with a little and pull it
thru with a pliers. |
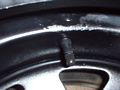 |
After
cleaning the bead areas up on the tire soap the inner bead and slide
it onto the rim. With the bead lock you don’t have to pry the outer
bead onto the rim. Tire changes and repairs just got much simpler
(except for the 32 bolts). I will caulk around the anti-coning ring
and the inner ring. Then I’ll put a bead on the top if the
anti-coning ring where it will meet the outer ring. This should seal
the dirt and water. |
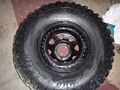 |
Install
the outer ring and the bolts. Hand start the nuts. Notice I forgot
the flat washers, which are important if you don’t want to mess up
the paint with the socket. Measure around the tire and outer bead to
center everything prior to tightening. For torquing I’m going to
play around with the air pressure regulator on my air compressor, a
3/8-air ratchet and a bolt through a dummy piece of metal until I
get the 15-psi torque at stall (check it with a torque wrench).
Ended up being 45 psi. This will speed up the 32 bolts per wheel
torquing process. I will alternate across the wheel and then go
around. |
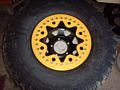 |
I’ll
inflate to 20-25 psi or so to make sure I seat the bead on the
backside. Then I’ll air down to around 10 psi or so and see how they
work. And they look sweet too. |
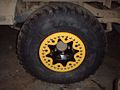 |
Impressions of the installation:
The anti-coning ring
is a good thing. I went around once and the torque is right. I
read a couple of installs were the anti-coning ring wasn’t used
and torquing was a nightmare. As I said earlier, these could
easily be made at a shop and added to a cheaper kit too. The air
ratchet worked out well. It would have been torture by hand (128
bolts total).
The inner ring ID is smaller than
it needs to be by an inch or so. Added weight with no value. The
pimp daddy rings added a little too. I think I would consider
weight more heavily if I did it again. The ID of both could be
the highest point in the outer ring pattern.
I thought I was getting nut-zerks
instead of nylock nuts. But the nuts weren’t that bad and they
won’t strip out. Also easy to get if I need another one.
Be sure to really clean the tire
beads. I had to remount one that was leaking there. It didn’t
look that bad but I should have spent the time and clean them
well.
Total bill of around $350
including paint, parts and freight.
If there are any
questions/comments, please send to
tratterman@mmm.com |
|
Updates:
I took them out this
weekend. They worked great at 10 psi. I don't think
I want to go much lower on air pressure with the ProComp 33s. I
managed to slip the bead on a rear one while trying to hammer
over a rock. Once I got home I took the air ratchet up to 90
psi (max) and gunned them all down. This was like 3/4 more turn
on each bolt. It should take care of any further issues. It
might be the ProComps bead area might not be as thick as other
tires (Swampers) so more torque is needed. With the anti-coning
ring you aren't deflecting the outer ring so gun 'um down.
Beadlocks + spin
balancer = angry Menieke technician. After much effort,
conventional balancing wasn't going to happen. The outside bead
is so much heavier than the inside . I did a little on-line
research and found that others had used BBs loose inside the
tires to keep the shakes down. Most used between 8 & 12 oz
(weight, not fluid) in each tire. My first thought was "BBs
rust". So I when with 12 oz of 7 1/2 shotgun shot in each tire
which won't rust. Smoothed it out nicely. I was upgrading to
some Swampers so adding it was easy. If you were adding and not
changing tires you could simply break the inside bead and pour
them in. By the way, I ran 6 psi in the 33 x 13.5 x 15 Super
Swamper LTBs on my last trip with no slippage. Talk about
hooking up.
|
|