Build Thread 77 CJ-7 Renegade Frame Off Restoration
WV 77Cj7
Jeeper
Hi guys- new to the forum here..I've been reading about the CJ7 's for months planning out the rebuild of a 77 I've acquired from my dad. Ive decided on this build thread to chronicle the restoration of this rust bucket.
A little history on the jeep- He bought it new back in 77 before he had any kids, and over the years it sat outside and slowly rusted away. I still don't know a whole lot about it since i haven't had a decent place to work on it, so once i figure out the stats on it will update my profile. However things I've picked up over the years- It came with the dealership installed Meyer plow option offered back in 77. I believe the plow is a 6.5'. Its in need of being restored as it was also left out to weather.
I recall a bunch of years ago dad pulled the jeep into the garage to try and slow the rusting taking place.. some patch panels were riveted in as he didn't have the time, tools or money to do the fix properly (couldn't stay permanently as a ford 1929 Model A calls the garage home). About 10 years ago the jeep was taken to a fab shop and the rear frame was repaired as it had badly rusted out like I've seen so many others do. The repair is strong.. once i yank the body ill take some pictures.
Everything was repainted and put back together. The soft top wreaked havoc on the jeep as it leaks during heavy down pours. The body is completely rusted out.. to the point its not safe to be driven any longer. I know this old jeep used to be a work horse, and has paid for itself 10 times over plowing. Always told myself growing up albeit i couldn't do anything at the time, id return it back to the way it looked the day it rolled off the dealership lot.
Some pictures:
Garage that i built this spring specially for this project (obviously not even done.. I'm anxious):
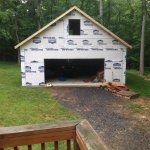
The Project:
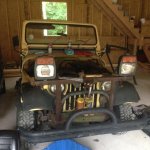
The day i picked it up from my dads it started giving me problems.. a quick napa trip fixed this one:
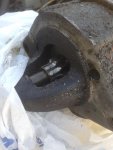
Future resting place for the next couple of years:
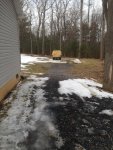
Meyer Plow:
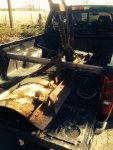
A little history on the jeep- He bought it new back in 77 before he had any kids, and over the years it sat outside and slowly rusted away. I still don't know a whole lot about it since i haven't had a decent place to work on it, so once i figure out the stats on it will update my profile. However things I've picked up over the years- It came with the dealership installed Meyer plow option offered back in 77. I believe the plow is a 6.5'. Its in need of being restored as it was also left out to weather.
I recall a bunch of years ago dad pulled the jeep into the garage to try and slow the rusting taking place.. some patch panels were riveted in as he didn't have the time, tools or money to do the fix properly (couldn't stay permanently as a ford 1929 Model A calls the garage home). About 10 years ago the jeep was taken to a fab shop and the rear frame was repaired as it had badly rusted out like I've seen so many others do. The repair is strong.. once i yank the body ill take some pictures.
Everything was repainted and put back together. The soft top wreaked havoc on the jeep as it leaks during heavy down pours. The body is completely rusted out.. to the point its not safe to be driven any longer. I know this old jeep used to be a work horse, and has paid for itself 10 times over plowing. Always told myself growing up albeit i couldn't do anything at the time, id return it back to the way it looked the day it rolled off the dealership lot.
Some pictures:
Garage that i built this spring specially for this project (obviously not even done.. I'm anxious):
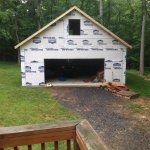
The Project:
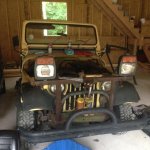
The day i picked it up from my dads it started giving me problems.. a quick napa trip fixed this one:
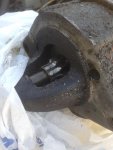
Future resting place for the next couple of years:
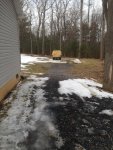
Meyer Plow:
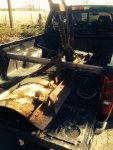