Build Thread Combat Barbie's CJ-7 rebuild
clear82star
Jeeper
I've owned several Jeeps in the past: 2 YJ's and a TJ. I've always wanted "the original round headlights", then I got stationed in Idaho, was finally able to buy a house (with attached garage), I couldn't think of a better time in my life to own one to work on. Here's some photos of what it looked like when I bought it. Took a lot to get it started just to get it home, and it died at every other red light… grrrr. It had been sitting for a while and (now I know) the engine was not well taken care of. I had a Jeep Patriot when I bought it (hence the side by side photo), but now own a Xterra.
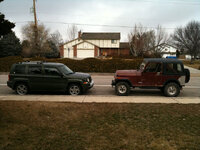
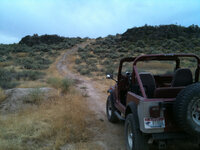
[FONT="]Here's the start/prep of my paint project:[/FONT]
[FONT="] [/FONT]
[FONT="]
[/FONT]
[FONT="]
[/FONT]
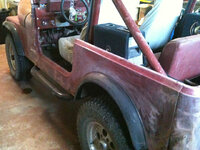
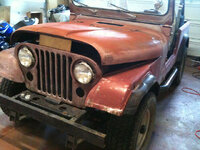
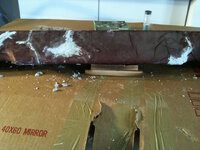
I chose Rustoleum hammered finish because I really like the finish (reminds me of my grandfather’s toolboxes and hides surface imperfections) and it’ll be easy to fix and scratches in the future. Plus you can paint right over rust with a little prep.
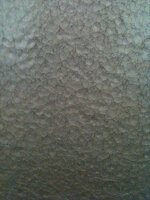
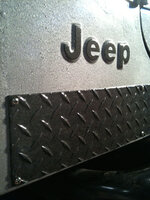
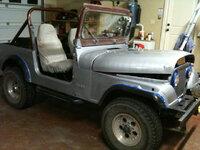
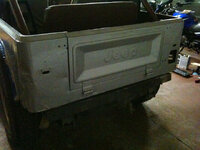
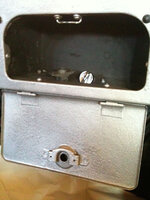
Then I prepped and painted the “interior” with rustoleum gloss and then rhino-lined it. I only have one picture of the rustoleum gloss prior to rhino lining it:
In the process I also made my own replacement handles. It’s a combination of 1 inch tubular webbing purchased at REI and flexible white PVC-? pipe found at Home Depot:
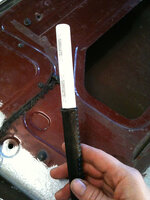
And salvaged the old seats (what can I say I’m cheap) by using suturing skillz to attach some vinyl to the worn out seat bottoms:
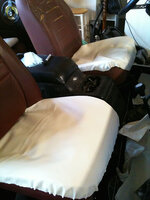
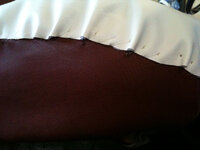
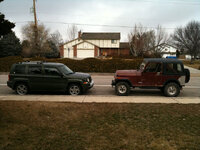
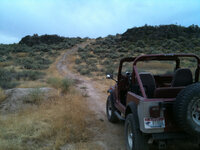
[FONT="]Here's the start/prep of my paint project:[/FONT]
[FONT="] [/FONT]
[FONT="]

[FONT="]
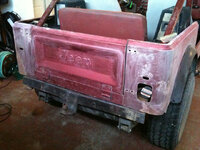
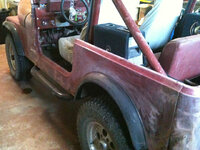
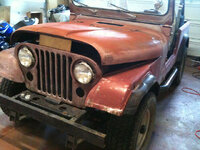

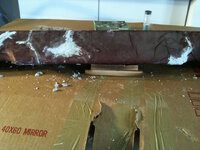
I chose Rustoleum hammered finish because I really like the finish (reminds me of my grandfather’s toolboxes and hides surface imperfections) and it’ll be easy to fix and scratches in the future. Plus you can paint right over rust with a little prep.
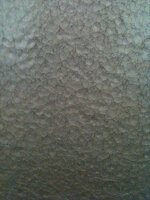
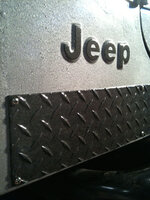
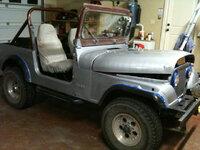
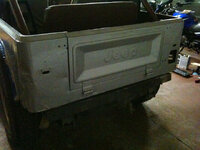

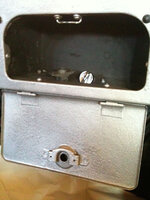
Then I prepped and painted the “interior” with rustoleum gloss and then rhino-lined it. I only have one picture of the rustoleum gloss prior to rhino lining it:

In the process I also made my own replacement handles. It’s a combination of 1 inch tubular webbing purchased at REI and flexible white PVC-? pipe found at Home Depot:
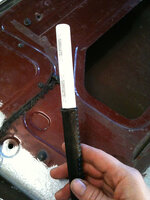
And salvaged the old seats (what can I say I’m cheap) by using suturing skillz to attach some vinyl to the worn out seat bottoms:
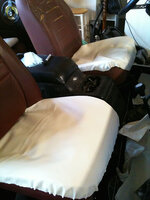
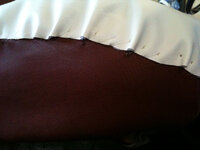
Last edited: