Build Thread AMC 401 Jeep CJ7 Drag Build with Tech Write-ups and lots of Pics
jarcher401
Jeeper
This is a build up that my father and I started when I was 14. I am now 23! Everything has been done by us with mostly my money. It has been a great learning experience which has helped me in my career and through trade school. Most of these posts are taken from the blog my dad started in 2006. 401 CJ7 JEEP BUILDUP: March 2006
So here we go.
March 2006
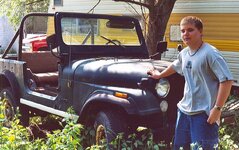
Here it is as we first layed eyes on it in May of 2004 at "The Jeep Shop" in Chester Springs, Pa. The Jeep Shop Originally from Florida, we checked the frame for rust and said ok. The owner would remove the 401 that was presently installed for a customer and we could have the rest for $500.00. The rest being a 400 turbo with quadra-trac. power steering, manual disc brakes and a Dana 30 up front and AMC20 in the rear. Along with a tilt column and tac dash, a totally waisted body and a good set of sellable tires and wheels.
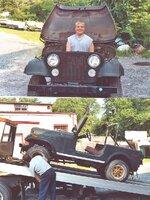
Here we are the weekend of 4th of July 2004. Now if that isn't a happy face nothing is. Powered by enthusiasm, I'd say. All we had to do to transport was to strap the torque converter in so it wouldn't fall out and load it up. That's Homer from "Moyers Car Care" of Friedensburg. Pa. doing the roll back thing, he's a real car guy that loves his job.
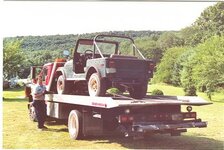
Here we are in Ghostbusters Headquarters, (got that sign from Burger King when the kids were younger, I think it's time to put it on Ebay.) Teardown began almost immediately, this is the easy part you really don't have to give a rat's a-- about damaging anything. After we got the front sheetmetal off, it was alot easier accessing the fire wall, wireing and brake stuff. Jeff is starting to get hooked on the smell of WD-40 though, it's like he can't get enough of it. We did tag any useable items and took lots of detailed photos for future reference. Believe me when I say it's easy to forget.
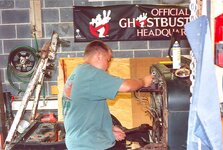
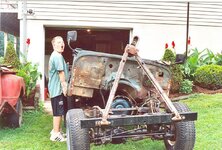
Well it just keeps going. Here we are two generations of Jeep building. Jeff senior on top in 1980 building his CJ5 and junior on bottom doing his thing at present. You just can't describe the feeling that comes from building a Jeep. The knowledge, respect, satisfaction, glory and bonding. All I can say is get your kids involved and they will gain all those traits. The memories that come out of something of this magnitude will last a life time. The parts hunting, bartering and trading. The new freinds that you will gain and places you will go that you normally wouldn't have if not for this mechanical wonder. And yes, even computer skills are learned when making up fake I.D.'s to get into those "no one under 18 allowed" u-pull junkyards. These are all life skills that will come in handy later on down the road.
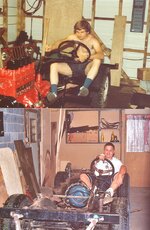
After we rolled the chassis back into "headquarters" (damn I gotta get rid of that sign) out came the 400 turbo and quadra trac. These will be rebuilt and reused, we are firm believers in this set-up. Have it in my J10 with over 200,000 trouble free miles. Reliability is great, you can still get parts and the full time traction is outstanding. Did I mention a 401 is going in this? oh yeh, that's the title of this blog. It was originally a AMC 304 jeep but a previous owner installed a 401 and the "Jeep Shop from Chester Springs" pulled the engine for a customer and sold us the rest for $500.00. I already had a rebuildable 401 core so wasn't worried. In the meantime we stumbled across a 7,000 mile rebuilt one. More on that later. We yanked the rears and leafsprings and was left with a bare frame. Found a couple of rust throughs, but all in the boxing sections, not in the major frame areas. This Jeep came out of Florida so it lead a better life than here in the northeast. We are also going to experiment with the 400 turbo by installing "switch pitch". This was used by G.M. from 1965 to 1967. What it is, is a variable stator torque converter which gives you hi stall, low stall in one unit. In other words hi performance and fuel economy at the flick of a switch. You can also split shift it as you manually run up through the gears. I have a couple of these transmissions laying around so I'll keep you updated. A shackle reversal up front along with YJ springs are also slated for this project. Want to go with wide track (56") axles. The front is no problem but the AMC20 offset differential rear was never made in wide track version, because wide track wasn't available until they stopped using quadra trac after 1979. I am not crazy about using spacers with 2 piece axles, so we'll see.
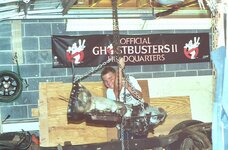
April 2006
Now that we have everything disassembled we can clean it up. I had said that this Jeep came out of Florida, well I think some of it came along for the ride. Then they wonder why the shorelines are diminishing. We must have washed out a ton of sand. Took a long garden hose and fished it up through the frame rail, worked really great. Found two areas that needed replacement with fresh metal. It was luckily confined to the boxed areas where the metal is of thinner gauge and not in anything structural. Simply cut out the bad areas and bent and shaped new material and welded in place. Be careful in doing the welding as not to get one area hot at one time, it is possible to bend a frame rail, rather stitch short areas and let cool before welding again. Take lots of measurements before and after. Haven't decided yet on what primer and paint to use to protect this yet. Would like to rust proof the insides of the rails. I don't know if any shops have a long wand to stick up the rail and spray it from the inside while dragging it out. Maybe if somebody out there knows of anything they can let me know. I have time for this yet, as we will be doing fabrication next.
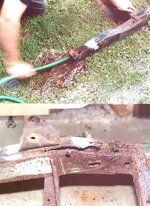
http://mountainoffroad.com/more.htm I ordered the unwelded kit version because it was cheaper and I wanted my son to learn some valuable welding.
The kit number is 7686-20 for $165.00 plus $24.29 shipping. To line everything up I stuck a threaded rod through both assemblies and again took lots of measurements. At the time I hadn't yet ordered the Wrangler springs for up front and since the CJ springs are narrower I used the back springs which are the same width as Wrangler springs to mock everything up. Make sure everything is square to the frame rails because if not this will only shorten the life of the bushings. Had to do a lot of shimming and tweaking (sledge hammer) to obtain this. For more info on the pros and cons on shackle reversals check out JP Magazine Jp Magazine at Four Wheeler Network they did a great article.
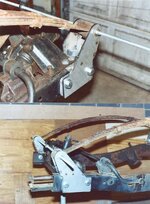
Well the springs finely got here. We wanted only a 2" lift for several reasons, safety, looks and the fact that a dropped pitman arm is not needed until after 2". We certainly didn't want to be bothered with bump steer, since this will be a daily driver and should be a pleasure to drive. We also wanted to go with 31" tires and with a shackle reversal kit it moves the front axle ahead by 1 1/2" which if you look at a side view of a stock CJ the front wheel is too far back in the wheel opening. So when you go to a larger tire you end up with clearance problems. The springs I got from my local Chysler dealer Outten in Hamburg, Pa. http://www.outtencars.com/location/hamburg-pa/index.jsp The service manager there is Brian Moyer who also runs Blue Mountain Jeep Alliance Club Blue Mountain Jeep Alliance He is a real Jeep guy and he advised me on the springs. We used Wrangler front springs part # OK-BDS-00420 and CJ rear springs part # OK-BDS-00425. These cost a total of $317.89 and was cheaper than a lift kit in which we would not have used many of the parts and also this way I could mix and match Wrangler/CJ springs. The Wrangler springs ride softer than the CJ and are also wider than CJ so we are hoping the rear springs are not too stiff. The reason we didn't go with Wrangler rear is because they are longer and I didn't want to have to mess with relocating spring mounts. I guess we will find out after it is on the road if we made a mistake or not. The rear part of the shackle reversal kit comes with a bushing tube that must be drilled and welded into the frame. The instructions for locating them are based on an assembled vehicle with all the weight. We didn't have that luxury. The shackle must be a little past centerline with all the weight on, it will bump and actually lift the Jeep when it tries to move back as the suspension travels. We actually had them too far front and when I got the bright idea to compress the springs with a bar clamp, the shackle moved too far back and ran out of travel. So I had to redrill the frame and weld in filler pieces in the original holes. Oh well, lessons will be learned. The bushing kit is from J.C Whitney JC Whitney Auto Parts & Auto Accessories - Car, Truck, Jeep, Motorcycle, VW, RV & ATV - Aftermarket Parts & Accessories catalog part #38166 or mfg. part # 1-1005 or 1-100 and cost $29.95. They are of the urethane type and I am sure will squeak. Gonna try and install some grease fittings to compansate.
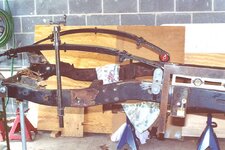
After hastily spending $250. On a wide track front Dana 30 so we could obtain the 56" track we still were not sure what to do with the rear. As I stated before an offset differential AMC20 was never produced in wide track, only a centered differential version was made after quadra trac was discontinued in 1979. So after some very precise measuring it was determined Dana 44 's from a quadra trac equipped Wagoneer could be used by shortening only one side of each housing. This could only have worked out better if we would not have bought the Dana 30 front. Needless to say we lost are asses on that purchase. So here is how it all went together. Front axle from 1979 quadra trac Wagoneer, shorten driverside by 4" and move spring perch in to give 27 1/4" spring center to center, (which is stock CJ). This will give you a track of 56", equal to stock CJ wide track. The original long driverside axle shaft can also be cut down and resplined, no need to have a custom axle made. The passengerside spring perch is cast into the housing and cannot be moved, but just happens to be in the right spot, and since we switched to Wrangler front springs they are the same width as Wagoneer. Otherwise the spring perches on a Dana 30 wide track are too narrow. This will also align the pinion angle up correctly. And remember that the shackle reversal kit moved the axle ahead 1 1/2", so if you stuck with a Dana 30 you would have to lengthen the front driveshaft 1 1/2", BUT and this is the neat part, a Dana 44 differential housing is 1 1/2" longer, OH YEH, a stock front driveshaft bolts right up, no lengthening. Use the Wagoneer spring u bolt plates and relocate the driverside shock mount to match the passengerside. Upper wide track bolt on shock mounts will have to replace the welded on narrow track shock mounts.
Okay, rear Dana 44 from 1979 quadra trac Wagoneer. Shorten the driverside by 2 3/4" and relocate the spring perches to the bottom. Again the stock axle can be shortened and resplined. The differential center line will still be off center by 1 1/2" from the Transfer Case but if you use a double carden driveshaft it will eliminate any vibration. The alternative to this was to shorten the passengerside by 1 1/2" and the driverside by 1 1/4" but then you would have to get custom axle shafts made for both sides. It worked out cheaper to have a double carden driveshaft made. The rear spring u bolt plates are stock CJ with the shock mounts with the u bolt holes elongated with a milling machine tc accommodate the bigger diameter axle.
So there you go strong Dana 44 's front and rear to handle all the torque from that 401. We stayed with the 6 bolt lug pattern because we had factory chrome wagon wheels and is a stronger set-up. This also gives you G.M. type front disc brake calipers which I prefer over the CJ type, a little easier to change pads. Keen eyes will see no rear brakes, you can stick with the drums or go with rear disc brakes like we are.
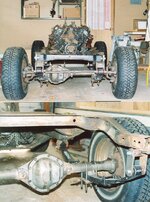
May 2006
This post will get a bit technical so if part numbers and details bore you, you might want to move on. If you think you might like to duplicate a steering set-up like this then I can save you a lot of aggravation and money on Advil, read on because this turned out pretty sweet.
Do in part to switching to Dana 44 's and keeping the Wagoneer spindles we ended up with only one tie rod end hole on the passenger side instead of two like the CJ. This proved to be troublesome in figuring out a tie rod set up. The Wagoneer tie rod has an intregrated tie rod end and would have to be shortened. We wanted to eliminate problems in the future when a tie rod end goes bad that another custom tie rod wouldn't have to be made plus the down time. Also with the shackle reversal moving the axle forward 1 1/2" brought the tie rod that much closer to the pitman arm. I see now why M.O.R.E.
Mountain Off Road- M.O.R.E. Manufacturer Direct Pricing on Jeep parts for Jeep YJ, Jeep CJ,Jeep TJ,Jeep JK and Jeep XJ models, quality jeep off road bumpers doesn't recommend a dropped pitman arm, it would obviously hit the tie rod. But we wanted to keep everything as parallel as possible to eliminate bump steer with the 2" lift and that meant a dropped arm. The dropped arm came from a 1987 Wrangler (square headlight) as did the beefier sway bar. The good old boys at B & S Auto Parts in Pine Grove loaned me an extra spicer parts book and after a few nights of reading and measuring I decided on a tie rod end incorporating a tapered hole for a drag link for a 1/2 ton Chevy. This gave me the same size ball end as a Wagoneer (bigger than a CJ) and the extra hole that was needed for the drag link that was eliminated off the spindle. (Spicer part number 401-1275. cost $18.29) The only problem is that this end is designed for the driver side of the Chevy thus the tapered hole, which was designed for a steering dampener was facing the wrong way, but happened to be smaller than the draglink tapered end. The hole had to be enlarged from the other end. So I did some searching for tapered reamers and found what I needed on Ebay. Damn isn't technology great? The reamer is an Xcut brand #5952, 1 1/2" taper per foot, bought from Ebay seller tltrades at his Ebay store XKUT for $47.99. I measured with a dial calipers what the large diameter of the hole should be and put a piece of tape on the reamer to get the depth, then mounted the tie rod end on a drill press and slowly reamed it out. The driverside tie rod end is a Spicer part number 401-1134, cost $34.89. The main tie rod is the only mildly custom part, but if you never damage it, will never need to be replaced. It is made from a 1979 Jeep J10. I have seen these in 2 versions totally straight or a bend to give extra clearance for the pitman arm, get the straight one. Cut off the end with the lefthand thread to a length of 32" and have the end rethreaded 7/8 - 18 left hand, this will be the only machine shop work performed, unless you have access to one. I am a machinist by trade so I was able to take it to work and wrote a program for a cnc lathe and thread it there. You will also have to put a bend in it, at a 13" centerline from the lefthand threaded end to clear the pitman arm. ( Of course do this after it's rethreaded or you wont be able to chuck it in a lathe.) The bend was perfomed with a hydraulic pipe bender from Harbor Freight Harbor Freight Tools ? Quality Tools at Discount Prices Since 1977 item number 32888-svga cost $74.99 and a little bit of heat. The tie rod end and tie rod are connected with Spicer adjuster sleeves part number 425-1002 cost $7.33 each. The drag link is a Spicer part number 405-1009 cost $46.00. The threaded end was shortened by 1" and rethreaded with a 7/8 - 18 righthand die purchased from MSC MSC Industrial Supply Co. | Find Power Tools, Hand Tools, Machine Tools & More part number 03938180 cost $32.62. A Spicer tie rod end, part number 401-1224 cost $49.88 and another adjuster sleeve rounds out the drag link. Connect this end to the Wrangler pitman arm. As you can see everything is pretty well parallel and as the suspension travels the pitman arm now clears the bend in the main tie rod. You can also install a shock dampener and brackets from a J10 with no clearance issues. The sway bar from the Wrangler can be mounted in the stock location on the frame, but the legs are straight unlike the curved down ones on a CJ requiring longer connecting links and is also wider. Well it just happens that unmodified links from a J10 are the correct length, but will have to be mounted on the inside of the swaybar instead of the outside. The tapered holes in the sway bar are facing the wrong way for this. You know that reamer that was purchased for the tie rod end? Yep, same size, just mount on a drill press and ream half way thru and the tapered bolt can then be used from the J10. This makes for one beefy set up with full adjustability, and readily available replacement parts that can be easily modified at home.
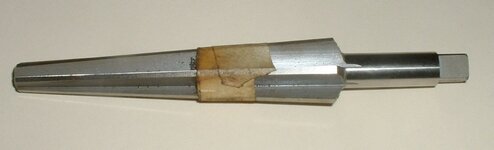
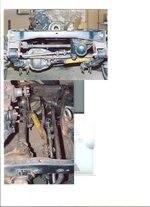
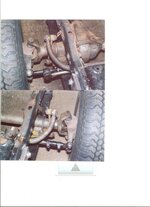
I told you earlier I would fill you in on a 401 that I stumbled on, so here it is. I called Jasper Motors jaspermotors.com about a AMC 258 i6 / 4.2l engine for my Eagle and just for the heck of it asked if they had any 401's. The guy laughed, said "the last core that came thru here was $1000.00." I told him about the CJ project, and he said "you should talk to my brother Ross Peterson, he's an AMC guru." Called him up and told him what we were into and he asked if we had the 401 built yet? No we aren't that far yet. Wanna buy one already built with 7000 miles on it? Turns out he built it himself for a Wagoneer he had, then ended up selling it minus the engine to a friend of his. It is built basically stock .030 over with premium parts and then balanced, has a rare R4B Edelbrock intake that was made for AMC to use in the SC/Ramblers. The torque curve is a little too high for the CJ, so we will be selling the intake. In the Wagoneer with a 400 Turbo and quadra trac, on a wet road moving at speed and dumped it into 2nd gear it would brake all 4 tires loose. By this time I'm figuring this thing is out of our price range, but had to ask how much? $3000.00!!
, I can't have one built for that. The bad part was he already sent adds out to AMC publications to sell it, but they didn't hit the news stands yet. So I had very little time to think it over. So needless to say I sent a down payment and picked it up 2 months later. He had a really nice run stand, so we could hear it run. You could actually put your hand on the valve cover and hardly feel it running that's how well balanced it is. Can't wait to get this thing installed.
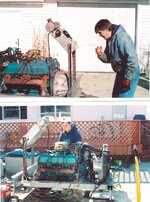
Moving to the rear we added a sway bar from Addco Manufacturing Home - Addco - Addco. They make sway bars for all sorts of vehicles. (Got one for my J10 years ago and they even made a special one for my CJ5 ). Part number OOK1-260-OU. 3/4" diameter and cost $134.00 for the CJ7 . I was a little leary that the bend in the center of it was going to clear the offset differential. Turned out the way they wanted it installed, this was going to interfere with our exhaust plans. It was to be installed with the center bend going over the driveshaft, fastened to the bottom of the frame rails, with the legs pointing towards the back and the ends fastened to the top of the leaf springs. Our plans for a dual in/dual out transverse muffler hung from the crossmember above the axle wasn't going to cut it. So I turned it around with the legs facing forward and the centered bend going over the top of the axle the way I originally thought it was to be installed. Luckily there was enough clearance for the offset differential. Had to fabricate mounts welded to the top of the axle tubes, and then another set of wedge shaped mounts welded under the frame rails. I used their u-brackets, but ran into a problem with their links not long enough. Did some measuring and determined that a set I had for the front of my 1967 Olds 442 were the perfect length. These are made by TRW http://www.trw.com/home/main/0,,,FF.html part number 18053. The rear shocks were gotten thru B & S Auto Parts. They were kind enough to copy spec pages out of their Monroe gatalog, MONROE SHOCKS & STRUTS :: Ride Safe with the Industry Leader of Ride Control Products took that and determined which ones we needed, they are part number 34802, cost $77.95.

How about a little driveshaft technology? Since we put a 2" suspension lift on this thing and with the longer pinion nose of the Dana 44 the already short drive shaft exceeded the 10 deg. max angle per a single u-joint. Plus looking down at the driveshaft it did not line up with the differential by 1 1/2". So now we have a compound angle to deal with. Everything I have read states that if the pinion angle is parallel with the output shaft and it doesn't exceeds 10 deg. a single u-joint can be used at each end. What a lot of people do if the angle does exceed 10 degs. is they tilt the pinion up so that it is parallel with the driveshaft. That's ok if you run a double carden joint on one end and a single on the pinion end. You see it takes 2 u-joints at the same angle to cancel out any vibration, as they turn they do not run at a steady speed, they run fast & slow. Therefore a second joint on the same end is needed to cancel out any vibration. When the driveshaft is parallel to the axle it will not set up a vibration. In our case we could have gotten away with tilting the pinion up if the pinion would have been in a straight line to the driveshaft looking down on it, but it was 1 1/2" off center. (compound angle) So we needed a double carden on each end to cancel out 2 different alignment issues. Several shops told me it would only vibrate slightly at different times and that a double carden was not needed. Well this thing is going to be street driven, and if it can be built with no vibration, then it will be built with no vibration. I knew of Tom Woods Tom Wood's Custom Drive Shafts - Tom Woods Custom Drive Shafts Custom Driveshafts Specialist but figured a local shop would be cheaper. The same shop that shortened the axles also did driveshafts. So I told Hartman Driveshaft and Axle, of Reading Pa. what I wanted. At first he claimed that we didn't need a double carden on each end that the vibration would be minimal. I persisted, even gave him some carden yokes to reuse and gave me a verbal quote of $500 to $600. Till it was all said and done the total was $944.73. OUCH!!! Now don't get me wrong, this shop does super quality work, did a great job on the axles, and takes pride in their workmanship. The killer driveshaft will never brake and the quality is impeccable, I'm just saying, shop around. I could have had the same shaft built by Woods and delivered to my door with a warranty for $650.00. Oh well, at least the front drive shaft is stock and only will require a rebuild.
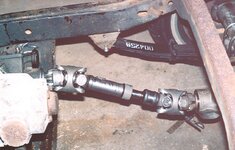
A little safety goes a long way in the shop, and we always try to practice that. Here is Jeff drilling out some reinforcement plates for the front shock mounts. The originals were shorter and welded to the frame, but since we switched to a wide trac axle we needed the longer shock towers as on the later Jeeps. I think the frame I took these off of had crush sleeves inside the frame rails, so we added these plates to eliminate any collapsing of the rails. Front shocks, again the good boys at B & S Auto Parts came thru with technical data so I could measure and come up with a standard shock. Also Monroe, part number 34821, cost $73.46. I took measurements off the donor frame but then moved them front to coincide with the shackle reversal moving the axle ahead. I also took a hole saw and drilled a drain hole at the bottom outside of the shock tower to eliminate any dirt and water being trapped between the shock mount and frame.
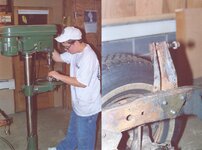
We picked up this 20 gal. poly. gas tank at the Blue Mountain Jeep Alliance Blue Mountain Jeep Alliance yearly flea market in Orwigsburg for $20.00 and a skid plate from I guess a Wrangler at EZ Pull & Save in New Ringgold. (Phone 570-386-2171). All we had to do was lower the skid plate and change it from two hold down straps to one. A length of steel was added to the second crossmember to achieve this. Also sliced a little off the right side to clear the leaf springs. A new rear crossmember was fabricated from 2 x 4 box tubing. Just cut holes in for the frame rails and slid it on. Take notice we had to reverse the shackle mounts to clear the new crossmember because it is bigger than the frame. The centerline of the shackle pivot point was kept the same so as not to disturb the geometry. The old tub was set on to scribe a radius on the ends of the crossmember to match the body. This will give a bit more protection for the corner of the body and I never liked how the factory crossmember looked anyhow. We are also thinking about notching out the crossmember for the exhaust, this should look pretty trick. We'll just take a piece of pipe and slice it in half and notch out the crossmember and weld it in place, sort of muscle car era look.
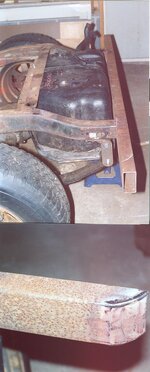
July 2006
Finally, "the body". Bought the tub, fenders and hood from Shell Valley out of Nebraska http://www.shellvalley.com/Replicas_and_Jeeps/Jeep/faq.asp I was a little leary buying sight unseen but they had a good reputation and the guy I dealt with "Dana" seemed pretty knowledgeable and up front. Little did I know but these guys are really into what they do. Shipping would have been $500.00 but I found out that they come into Carlisle for the kit car show with their cobra bodies so I asked if they had room to bring my body along and they obliged and only charged me $300.00 for shipping. Body cost was $2,174.00. Well I must say I was very happy when I saw the quality of the body. Double wall construction. All the other bodies I have seen had one downfall, the upper back corner of the door opening, where the door latch is, flexed and made shutting the door a chore. I can tell you right now, this one don't give at all. The tailgate opening was my other concern, would the stock steel tailgate fit. I positioned ours and had a nice even gap all the way around. I can only hope the steel doors will fit the same. They did bring a fiberglass windshield along at my request to look at. They explained that if you run with a soft top or no top that they have a tendency to flex, but is alright with a hardtop. The quality again was first rate but with the chances of this hardtop coming off I passed in favor of a steel one. I just know it will rust, you just can't seal them totally. Maybe I'll just have to try a little harder to convince Jeffrey to leave the hardtop on. To transport the body I cut some 2 x 6's to fit across the bedliner and ran straps to the hold downs at the front and back near the floor, this way the box for the hood slipped right underneath and the fender boxes I put in the tub. Next post I'll have some installation tips.
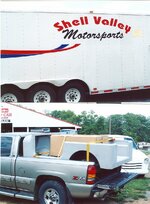
ust thought I would show you the one man lifting device I made. I took a length of rectangular tubing and sliced it (channel would also work I just didn't have any) then welded on some slotted pieces to hook a length of chain into. A piece of 3/4" thick wood goes between the body and the tubing (now channel) to protect the body. A length of pipe longer than the body is wide was cut with a piece of metal with a hole in to fit my chain hoist was welded in the middle along with 2 bolts (heads down) to keep the length of chain from sliding on each end spaced just a little wider than the body. The center link of each chain was painted red for easy identification of the center link. Just hook the ends onto the bracket and run up over the pipe onto the bolts. The channels can be slid front or back to find the balance point of the body.
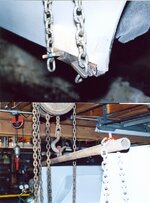
Lost no time in placing the body on the frame, (just had to see how it looked). Even the rollbar fits well. I had gotten an installation video from 4 wheel drive hardware Jeep Wrangler accessories, Jeep Wrangler parts & Jeep body parts to get a little educated, and picked up a few things from it. The way they start out, they place four 2" spacers at the middle mounts and measure the remaining mounts, then mount the hood, then the fenders and grille and whatever length mount the grille takes that's what is is. My problem with this method is that it wont always cosmetically look ok. I wound up with way too much of a gap at the rear crossmember and next to none at the grille. Trying to correct this we kept adjusting the mount lengths in the middle which kept rocking the gaps back and forth. I finally got tired of doing this so instead I started with the rear crossmember, Got a nice 1/2" gap then put two 1" mounts up front as a starting point. I checked for clearance in the middle which was ok. Then the hood was mounted, the fenders and the grille. The grille mount was adjusted until it was cosmetically correct by lifting the front of the tub which in turn allowed the front body mounts to fall into place. Now that the front and back where correct we made sure everything cleared in the middle, measured the rest of the body mounts and cut them. Now keep in mind we put no body lift on this, if you do, it can still be done using this method with a lot less hassle. Reinforcing strips are used at the mounting points of the body and fenders. This made for a very ridgid setup, you could actually lift at the grille and lift the front of the body if needed. I can remember going to shows and seeing Jeeps with no body lift with a very unsightly gap at the rear crossmember or at the grille. If you start in the back this can be elliminated. Again I can't say enough about this Shell Valley body. Give them a call or check them out on the web. Shell Valley Classic Wheels, Inc.
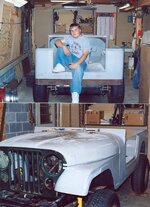
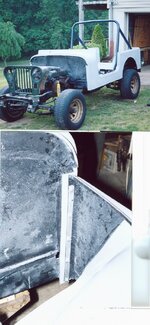
In this view you can see the difference that the shackle reversal made in moving the front axle ahead, centers the wheel a little better in the opening. Can't wait to get those 31's mounted on those factory chrome wagon wheels. Had to cut out for the taller wide track shock mounts, a saber saw made quick work of this. Start out by cutting only a little at a time. It's easier to remove than to add. We will probably add a rubber shield to cover the outside of the shock and mount to help cut down dirt from entering into the engine bay.
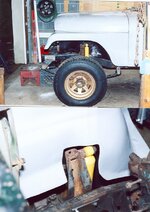
August 2006
Jeffrey wanted some kind of hood scoop for the CJ and we had looked at some "Bulge Hoods" which all had a raised center section but it just took away from the classic design that he wanted to retain. So the search was on. We needed something that would be close to the shape of the center raised section of a stock hood and the 401 emblems had to fit on the sides (that was a must) . These emblems were puchased off Ebay from member "berg102" eBay Feedback Profile for berg102. These are really top quality metal (not plastic) hand painted U.S. made. The hood scoop came from CJ Pony out of Harrisburg, Pa. Ford Mustang Parts | Mustang Parts & Accessories | CJ Pony Parts. This is strickly a Ford Mustang store so we felt a little out of place, but the people could not have been nicer. They even went out to the dumpster for a piece of cardboard so we could scribe a footprint of the scoop so we could see before we bought it, if it would fit the hood. The hood scoop had to clear the Laredo stripes we planned for the Jeep. If we would use it with the opening towards the front it would interfear with the stripes. So Jeffrey decides "how about cowl induction"? So we turned it around with the opening in the back and everything should clear. We might order a stripe kit first to make sure. As you can see this thing comes with studs glassed in so installation should be a snap. Stay tuned for the installation.
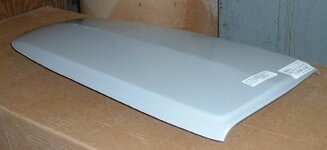
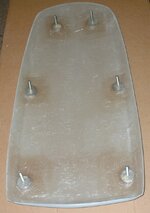
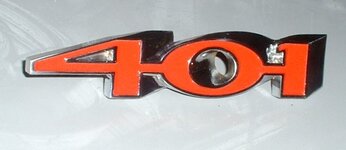
So here we go.
March 2006
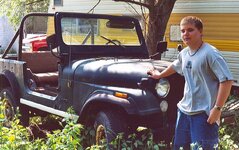
Here it is as we first layed eyes on it in May of 2004 at "The Jeep Shop" in Chester Springs, Pa. The Jeep Shop Originally from Florida, we checked the frame for rust and said ok. The owner would remove the 401 that was presently installed for a customer and we could have the rest for $500.00. The rest being a 400 turbo with quadra-trac. power steering, manual disc brakes and a Dana 30 up front and AMC20 in the rear. Along with a tilt column and tac dash, a totally waisted body and a good set of sellable tires and wheels.
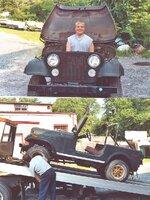
Here we are the weekend of 4th of July 2004. Now if that isn't a happy face nothing is. Powered by enthusiasm, I'd say. All we had to do to transport was to strap the torque converter in so it wouldn't fall out and load it up. That's Homer from "Moyers Car Care" of Friedensburg. Pa. doing the roll back thing, he's a real car guy that loves his job.
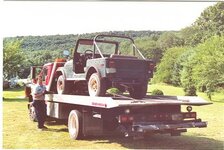
Here we are in Ghostbusters Headquarters, (got that sign from Burger King when the kids were younger, I think it's time to put it on Ebay.) Teardown began almost immediately, this is the easy part you really don't have to give a rat's a-- about damaging anything. After we got the front sheetmetal off, it was alot easier accessing the fire wall, wireing and brake stuff. Jeff is starting to get hooked on the smell of WD-40 though, it's like he can't get enough of it. We did tag any useable items and took lots of detailed photos for future reference. Believe me when I say it's easy to forget.
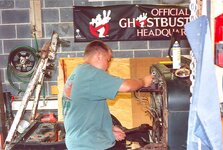
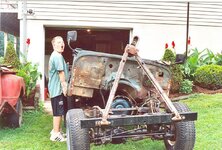
Well it just keeps going. Here we are two generations of Jeep building. Jeff senior on top in 1980 building his CJ5 and junior on bottom doing his thing at present. You just can't describe the feeling that comes from building a Jeep. The knowledge, respect, satisfaction, glory and bonding. All I can say is get your kids involved and they will gain all those traits. The memories that come out of something of this magnitude will last a life time. The parts hunting, bartering and trading. The new freinds that you will gain and places you will go that you normally wouldn't have if not for this mechanical wonder. And yes, even computer skills are learned when making up fake I.D.'s to get into those "no one under 18 allowed" u-pull junkyards. These are all life skills that will come in handy later on down the road.
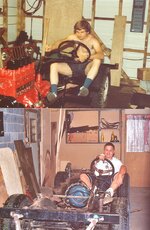
After we rolled the chassis back into "headquarters" (damn I gotta get rid of that sign) out came the 400 turbo and quadra trac. These will be rebuilt and reused, we are firm believers in this set-up. Have it in my J10 with over 200,000 trouble free miles. Reliability is great, you can still get parts and the full time traction is outstanding. Did I mention a 401 is going in this? oh yeh, that's the title of this blog. It was originally a AMC 304 jeep but a previous owner installed a 401 and the "Jeep Shop from Chester Springs" pulled the engine for a customer and sold us the rest for $500.00. I already had a rebuildable 401 core so wasn't worried. In the meantime we stumbled across a 7,000 mile rebuilt one. More on that later. We yanked the rears and leafsprings and was left with a bare frame. Found a couple of rust throughs, but all in the boxing sections, not in the major frame areas. This Jeep came out of Florida so it lead a better life than here in the northeast. We are also going to experiment with the 400 turbo by installing "switch pitch". This was used by G.M. from 1965 to 1967. What it is, is a variable stator torque converter which gives you hi stall, low stall in one unit. In other words hi performance and fuel economy at the flick of a switch. You can also split shift it as you manually run up through the gears. I have a couple of these transmissions laying around so I'll keep you updated. A shackle reversal up front along with YJ springs are also slated for this project. Want to go with wide track (56") axles. The front is no problem but the AMC20 offset differential rear was never made in wide track version, because wide track wasn't available until they stopped using quadra trac after 1979. I am not crazy about using spacers with 2 piece axles, so we'll see.
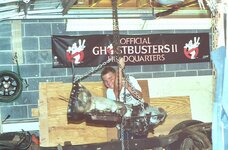
April 2006
Now that we have everything disassembled we can clean it up. I had said that this Jeep came out of Florida, well I think some of it came along for the ride. Then they wonder why the shorelines are diminishing. We must have washed out a ton of sand. Took a long garden hose and fished it up through the frame rail, worked really great. Found two areas that needed replacement with fresh metal. It was luckily confined to the boxed areas where the metal is of thinner gauge and not in anything structural. Simply cut out the bad areas and bent and shaped new material and welded in place. Be careful in doing the welding as not to get one area hot at one time, it is possible to bend a frame rail, rather stitch short areas and let cool before welding again. Take lots of measurements before and after. Haven't decided yet on what primer and paint to use to protect this yet. Would like to rust proof the insides of the rails. I don't know if any shops have a long wand to stick up the rail and spray it from the inside while dragging it out. Maybe if somebody out there knows of anything they can let me know. I have time for this yet, as we will be doing fabrication next.
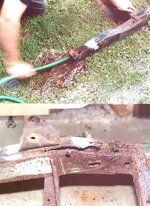
http://mountainoffroad.com/more.htm I ordered the unwelded kit version because it was cheaper and I wanted my son to learn some valuable welding.
The kit number is 7686-20 for $165.00 plus $24.29 shipping. To line everything up I stuck a threaded rod through both assemblies and again took lots of measurements. At the time I hadn't yet ordered the Wrangler springs for up front and since the CJ springs are narrower I used the back springs which are the same width as Wrangler springs to mock everything up. Make sure everything is square to the frame rails because if not this will only shorten the life of the bushings. Had to do a lot of shimming and tweaking (sledge hammer) to obtain this. For more info on the pros and cons on shackle reversals check out JP Magazine Jp Magazine at Four Wheeler Network they did a great article.
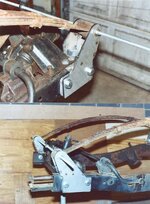
Well the springs finely got here. We wanted only a 2" lift for several reasons, safety, looks and the fact that a dropped pitman arm is not needed until after 2". We certainly didn't want to be bothered with bump steer, since this will be a daily driver and should be a pleasure to drive. We also wanted to go with 31" tires and with a shackle reversal kit it moves the front axle ahead by 1 1/2" which if you look at a side view of a stock CJ the front wheel is too far back in the wheel opening. So when you go to a larger tire you end up with clearance problems. The springs I got from my local Chysler dealer Outten in Hamburg, Pa. http://www.outtencars.com/location/hamburg-pa/index.jsp The service manager there is Brian Moyer who also runs Blue Mountain Jeep Alliance Club Blue Mountain Jeep Alliance He is a real Jeep guy and he advised me on the springs. We used Wrangler front springs part # OK-BDS-00420 and CJ rear springs part # OK-BDS-00425. These cost a total of $317.89 and was cheaper than a lift kit in which we would not have used many of the parts and also this way I could mix and match Wrangler/CJ springs. The Wrangler springs ride softer than the CJ and are also wider than CJ so we are hoping the rear springs are not too stiff. The reason we didn't go with Wrangler rear is because they are longer and I didn't want to have to mess with relocating spring mounts. I guess we will find out after it is on the road if we made a mistake or not. The rear part of the shackle reversal kit comes with a bushing tube that must be drilled and welded into the frame. The instructions for locating them are based on an assembled vehicle with all the weight. We didn't have that luxury. The shackle must be a little past centerline with all the weight on, it will bump and actually lift the Jeep when it tries to move back as the suspension travels. We actually had them too far front and when I got the bright idea to compress the springs with a bar clamp, the shackle moved too far back and ran out of travel. So I had to redrill the frame and weld in filler pieces in the original holes. Oh well, lessons will be learned. The bushing kit is from J.C Whitney JC Whitney Auto Parts & Auto Accessories - Car, Truck, Jeep, Motorcycle, VW, RV & ATV - Aftermarket Parts & Accessories catalog part #38166 or mfg. part # 1-1005 or 1-100 and cost $29.95. They are of the urethane type and I am sure will squeak. Gonna try and install some grease fittings to compansate.
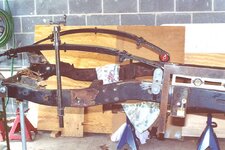
After hastily spending $250. On a wide track front Dana 30 so we could obtain the 56" track we still were not sure what to do with the rear. As I stated before an offset differential AMC20 was never produced in wide track, only a centered differential version was made after quadra trac was discontinued in 1979. So after some very precise measuring it was determined Dana 44 's from a quadra trac equipped Wagoneer could be used by shortening only one side of each housing. This could only have worked out better if we would not have bought the Dana 30 front. Needless to say we lost are asses on that purchase. So here is how it all went together. Front axle from 1979 quadra trac Wagoneer, shorten driverside by 4" and move spring perch in to give 27 1/4" spring center to center, (which is stock CJ). This will give you a track of 56", equal to stock CJ wide track. The original long driverside axle shaft can also be cut down and resplined, no need to have a custom axle made. The passengerside spring perch is cast into the housing and cannot be moved, but just happens to be in the right spot, and since we switched to Wrangler front springs they are the same width as Wagoneer. Otherwise the spring perches on a Dana 30 wide track are too narrow. This will also align the pinion angle up correctly. And remember that the shackle reversal kit moved the axle ahead 1 1/2", so if you stuck with a Dana 30 you would have to lengthen the front driveshaft 1 1/2", BUT and this is the neat part, a Dana 44 differential housing is 1 1/2" longer, OH YEH, a stock front driveshaft bolts right up, no lengthening. Use the Wagoneer spring u bolt plates and relocate the driverside shock mount to match the passengerside. Upper wide track bolt on shock mounts will have to replace the welded on narrow track shock mounts.
Okay, rear Dana 44 from 1979 quadra trac Wagoneer. Shorten the driverside by 2 3/4" and relocate the spring perches to the bottom. Again the stock axle can be shortened and resplined. The differential center line will still be off center by 1 1/2" from the Transfer Case but if you use a double carden driveshaft it will eliminate any vibration. The alternative to this was to shorten the passengerside by 1 1/2" and the driverside by 1 1/4" but then you would have to get custom axle shafts made for both sides. It worked out cheaper to have a double carden driveshaft made. The rear spring u bolt plates are stock CJ with the shock mounts with the u bolt holes elongated with a milling machine tc accommodate the bigger diameter axle.
So there you go strong Dana 44 's front and rear to handle all the torque from that 401. We stayed with the 6 bolt lug pattern because we had factory chrome wagon wheels and is a stronger set-up. This also gives you G.M. type front disc brake calipers which I prefer over the CJ type, a little easier to change pads. Keen eyes will see no rear brakes, you can stick with the drums or go with rear disc brakes like we are.
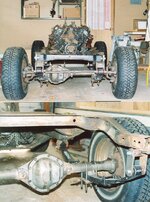
May 2006
This post will get a bit technical so if part numbers and details bore you, you might want to move on. If you think you might like to duplicate a steering set-up like this then I can save you a lot of aggravation and money on Advil, read on because this turned out pretty sweet.
Do in part to switching to Dana 44 's and keeping the Wagoneer spindles we ended up with only one tie rod end hole on the passenger side instead of two like the CJ. This proved to be troublesome in figuring out a tie rod set up. The Wagoneer tie rod has an intregrated tie rod end and would have to be shortened. We wanted to eliminate problems in the future when a tie rod end goes bad that another custom tie rod wouldn't have to be made plus the down time. Also with the shackle reversal moving the axle forward 1 1/2" brought the tie rod that much closer to the pitman arm. I see now why M.O.R.E.
Mountain Off Road- M.O.R.E. Manufacturer Direct Pricing on Jeep parts for Jeep YJ, Jeep CJ,Jeep TJ,Jeep JK and Jeep XJ models, quality jeep off road bumpers doesn't recommend a dropped pitman arm, it would obviously hit the tie rod. But we wanted to keep everything as parallel as possible to eliminate bump steer with the 2" lift and that meant a dropped arm. The dropped arm came from a 1987 Wrangler (square headlight) as did the beefier sway bar. The good old boys at B & S Auto Parts in Pine Grove loaned me an extra spicer parts book and after a few nights of reading and measuring I decided on a tie rod end incorporating a tapered hole for a drag link for a 1/2 ton Chevy. This gave me the same size ball end as a Wagoneer (bigger than a CJ) and the extra hole that was needed for the drag link that was eliminated off the spindle. (Spicer part number 401-1275. cost $18.29) The only problem is that this end is designed for the driver side of the Chevy thus the tapered hole, which was designed for a steering dampener was facing the wrong way, but happened to be smaller than the draglink tapered end. The hole had to be enlarged from the other end. So I did some searching for tapered reamers and found what I needed on Ebay. Damn isn't technology great? The reamer is an Xcut brand #5952, 1 1/2" taper per foot, bought from Ebay seller tltrades at his Ebay store XKUT for $47.99. I measured with a dial calipers what the large diameter of the hole should be and put a piece of tape on the reamer to get the depth, then mounted the tie rod end on a drill press and slowly reamed it out. The driverside tie rod end is a Spicer part number 401-1134, cost $34.89. The main tie rod is the only mildly custom part, but if you never damage it, will never need to be replaced. It is made from a 1979 Jeep J10. I have seen these in 2 versions totally straight or a bend to give extra clearance for the pitman arm, get the straight one. Cut off the end with the lefthand thread to a length of 32" and have the end rethreaded 7/8 - 18 left hand, this will be the only machine shop work performed, unless you have access to one. I am a machinist by trade so I was able to take it to work and wrote a program for a cnc lathe and thread it there. You will also have to put a bend in it, at a 13" centerline from the lefthand threaded end to clear the pitman arm. ( Of course do this after it's rethreaded or you wont be able to chuck it in a lathe.) The bend was perfomed with a hydraulic pipe bender from Harbor Freight Harbor Freight Tools ? Quality Tools at Discount Prices Since 1977 item number 32888-svga cost $74.99 and a little bit of heat. The tie rod end and tie rod are connected with Spicer adjuster sleeves part number 425-1002 cost $7.33 each. The drag link is a Spicer part number 405-1009 cost $46.00. The threaded end was shortened by 1" and rethreaded with a 7/8 - 18 righthand die purchased from MSC MSC Industrial Supply Co. | Find Power Tools, Hand Tools, Machine Tools & More part number 03938180 cost $32.62. A Spicer tie rod end, part number 401-1224 cost $49.88 and another adjuster sleeve rounds out the drag link. Connect this end to the Wrangler pitman arm. As you can see everything is pretty well parallel and as the suspension travels the pitman arm now clears the bend in the main tie rod. You can also install a shock dampener and brackets from a J10 with no clearance issues. The sway bar from the Wrangler can be mounted in the stock location on the frame, but the legs are straight unlike the curved down ones on a CJ requiring longer connecting links and is also wider. Well it just happens that unmodified links from a J10 are the correct length, but will have to be mounted on the inside of the swaybar instead of the outside. The tapered holes in the sway bar are facing the wrong way for this. You know that reamer that was purchased for the tie rod end? Yep, same size, just mount on a drill press and ream half way thru and the tapered bolt can then be used from the J10. This makes for one beefy set up with full adjustability, and readily available replacement parts that can be easily modified at home.
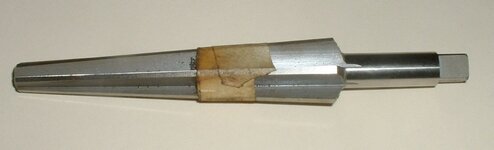
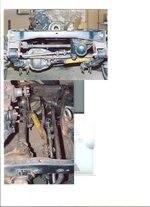
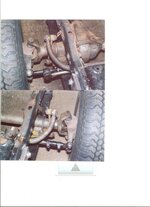
I told you earlier I would fill you in on a 401 that I stumbled on, so here it is. I called Jasper Motors jaspermotors.com about a AMC 258 i6 / 4.2l engine for my Eagle and just for the heck of it asked if they had any 401's. The guy laughed, said "the last core that came thru here was $1000.00." I told him about the CJ project, and he said "you should talk to my brother Ross Peterson, he's an AMC guru." Called him up and told him what we were into and he asked if we had the 401 built yet? No we aren't that far yet. Wanna buy one already built with 7000 miles on it? Turns out he built it himself for a Wagoneer he had, then ended up selling it minus the engine to a friend of his. It is built basically stock .030 over with premium parts and then balanced, has a rare R4B Edelbrock intake that was made for AMC to use in the SC/Ramblers. The torque curve is a little too high for the CJ, so we will be selling the intake. In the Wagoneer with a 400 Turbo and quadra trac, on a wet road moving at speed and dumped it into 2nd gear it would brake all 4 tires loose. By this time I'm figuring this thing is out of our price range, but had to ask how much? $3000.00!!

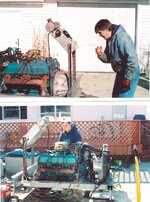
Moving to the rear we added a sway bar from Addco Manufacturing Home - Addco - Addco. They make sway bars for all sorts of vehicles. (Got one for my J10 years ago and they even made a special one for my CJ5 ). Part number OOK1-260-OU. 3/4" diameter and cost $134.00 for the CJ7 . I was a little leary that the bend in the center of it was going to clear the offset differential. Turned out the way they wanted it installed, this was going to interfere with our exhaust plans. It was to be installed with the center bend going over the driveshaft, fastened to the bottom of the frame rails, with the legs pointing towards the back and the ends fastened to the top of the leaf springs. Our plans for a dual in/dual out transverse muffler hung from the crossmember above the axle wasn't going to cut it. So I turned it around with the legs facing forward and the centered bend going over the top of the axle the way I originally thought it was to be installed. Luckily there was enough clearance for the offset differential. Had to fabricate mounts welded to the top of the axle tubes, and then another set of wedge shaped mounts welded under the frame rails. I used their u-brackets, but ran into a problem with their links not long enough. Did some measuring and determined that a set I had for the front of my 1967 Olds 442 were the perfect length. These are made by TRW http://www.trw.com/home/main/0,,,FF.html part number 18053. The rear shocks were gotten thru B & S Auto Parts. They were kind enough to copy spec pages out of their Monroe gatalog, MONROE SHOCKS & STRUTS :: Ride Safe with the Industry Leader of Ride Control Products took that and determined which ones we needed, they are part number 34802, cost $77.95.

How about a little driveshaft technology? Since we put a 2" suspension lift on this thing and with the longer pinion nose of the Dana 44 the already short drive shaft exceeded the 10 deg. max angle per a single u-joint. Plus looking down at the driveshaft it did not line up with the differential by 1 1/2". So now we have a compound angle to deal with. Everything I have read states that if the pinion angle is parallel with the output shaft and it doesn't exceeds 10 deg. a single u-joint can be used at each end. What a lot of people do if the angle does exceed 10 degs. is they tilt the pinion up so that it is parallel with the driveshaft. That's ok if you run a double carden joint on one end and a single on the pinion end. You see it takes 2 u-joints at the same angle to cancel out any vibration, as they turn they do not run at a steady speed, they run fast & slow. Therefore a second joint on the same end is needed to cancel out any vibration. When the driveshaft is parallel to the axle it will not set up a vibration. In our case we could have gotten away with tilting the pinion up if the pinion would have been in a straight line to the driveshaft looking down on it, but it was 1 1/2" off center. (compound angle) So we needed a double carden on each end to cancel out 2 different alignment issues. Several shops told me it would only vibrate slightly at different times and that a double carden was not needed. Well this thing is going to be street driven, and if it can be built with no vibration, then it will be built with no vibration. I knew of Tom Woods Tom Wood's Custom Drive Shafts - Tom Woods Custom Drive Shafts Custom Driveshafts Specialist but figured a local shop would be cheaper. The same shop that shortened the axles also did driveshafts. So I told Hartman Driveshaft and Axle, of Reading Pa. what I wanted. At first he claimed that we didn't need a double carden on each end that the vibration would be minimal. I persisted, even gave him some carden yokes to reuse and gave me a verbal quote of $500 to $600. Till it was all said and done the total was $944.73. OUCH!!! Now don't get me wrong, this shop does super quality work, did a great job on the axles, and takes pride in their workmanship. The killer driveshaft will never brake and the quality is impeccable, I'm just saying, shop around. I could have had the same shaft built by Woods and delivered to my door with a warranty for $650.00. Oh well, at least the front drive shaft is stock and only will require a rebuild.
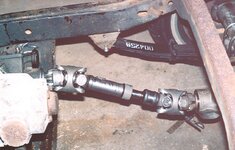
A little safety goes a long way in the shop, and we always try to practice that. Here is Jeff drilling out some reinforcement plates for the front shock mounts. The originals were shorter and welded to the frame, but since we switched to a wide trac axle we needed the longer shock towers as on the later Jeeps. I think the frame I took these off of had crush sleeves inside the frame rails, so we added these plates to eliminate any collapsing of the rails. Front shocks, again the good boys at B & S Auto Parts came thru with technical data so I could measure and come up with a standard shock. Also Monroe, part number 34821, cost $73.46. I took measurements off the donor frame but then moved them front to coincide with the shackle reversal moving the axle ahead. I also took a hole saw and drilled a drain hole at the bottom outside of the shock tower to eliminate any dirt and water being trapped between the shock mount and frame.
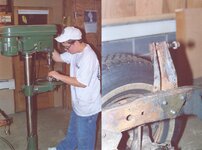
We picked up this 20 gal. poly. gas tank at the Blue Mountain Jeep Alliance Blue Mountain Jeep Alliance yearly flea market in Orwigsburg for $20.00 and a skid plate from I guess a Wrangler at EZ Pull & Save in New Ringgold. (Phone 570-386-2171). All we had to do was lower the skid plate and change it from two hold down straps to one. A length of steel was added to the second crossmember to achieve this. Also sliced a little off the right side to clear the leaf springs. A new rear crossmember was fabricated from 2 x 4 box tubing. Just cut holes in for the frame rails and slid it on. Take notice we had to reverse the shackle mounts to clear the new crossmember because it is bigger than the frame. The centerline of the shackle pivot point was kept the same so as not to disturb the geometry. The old tub was set on to scribe a radius on the ends of the crossmember to match the body. This will give a bit more protection for the corner of the body and I never liked how the factory crossmember looked anyhow. We are also thinking about notching out the crossmember for the exhaust, this should look pretty trick. We'll just take a piece of pipe and slice it in half and notch out the crossmember and weld it in place, sort of muscle car era look.
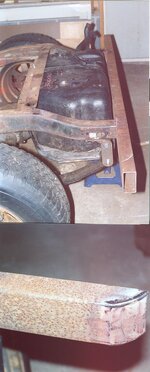
July 2006
Finally, "the body". Bought the tub, fenders and hood from Shell Valley out of Nebraska http://www.shellvalley.com/Replicas_and_Jeeps/Jeep/faq.asp I was a little leary buying sight unseen but they had a good reputation and the guy I dealt with "Dana" seemed pretty knowledgeable and up front. Little did I know but these guys are really into what they do. Shipping would have been $500.00 but I found out that they come into Carlisle for the kit car show with their cobra bodies so I asked if they had room to bring my body along and they obliged and only charged me $300.00 for shipping. Body cost was $2,174.00. Well I must say I was very happy when I saw the quality of the body. Double wall construction. All the other bodies I have seen had one downfall, the upper back corner of the door opening, where the door latch is, flexed and made shutting the door a chore. I can tell you right now, this one don't give at all. The tailgate opening was my other concern, would the stock steel tailgate fit. I positioned ours and had a nice even gap all the way around. I can only hope the steel doors will fit the same. They did bring a fiberglass windshield along at my request to look at. They explained that if you run with a soft top or no top that they have a tendency to flex, but is alright with a hardtop. The quality again was first rate but with the chances of this hardtop coming off I passed in favor of a steel one. I just know it will rust, you just can't seal them totally. Maybe I'll just have to try a little harder to convince Jeffrey to leave the hardtop on. To transport the body I cut some 2 x 6's to fit across the bedliner and ran straps to the hold downs at the front and back near the floor, this way the box for the hood slipped right underneath and the fender boxes I put in the tub. Next post I'll have some installation tips.
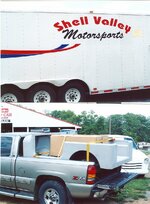
ust thought I would show you the one man lifting device I made. I took a length of rectangular tubing and sliced it (channel would also work I just didn't have any) then welded on some slotted pieces to hook a length of chain into. A piece of 3/4" thick wood goes between the body and the tubing (now channel) to protect the body. A length of pipe longer than the body is wide was cut with a piece of metal with a hole in to fit my chain hoist was welded in the middle along with 2 bolts (heads down) to keep the length of chain from sliding on each end spaced just a little wider than the body. The center link of each chain was painted red for easy identification of the center link. Just hook the ends onto the bracket and run up over the pipe onto the bolts. The channels can be slid front or back to find the balance point of the body.
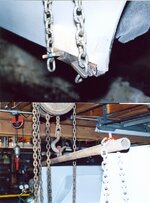
Lost no time in placing the body on the frame, (just had to see how it looked). Even the rollbar fits well. I had gotten an installation video from 4 wheel drive hardware Jeep Wrangler accessories, Jeep Wrangler parts & Jeep body parts to get a little educated, and picked up a few things from it. The way they start out, they place four 2" spacers at the middle mounts and measure the remaining mounts, then mount the hood, then the fenders and grille and whatever length mount the grille takes that's what is is. My problem with this method is that it wont always cosmetically look ok. I wound up with way too much of a gap at the rear crossmember and next to none at the grille. Trying to correct this we kept adjusting the mount lengths in the middle which kept rocking the gaps back and forth. I finally got tired of doing this so instead I started with the rear crossmember, Got a nice 1/2" gap then put two 1" mounts up front as a starting point. I checked for clearance in the middle which was ok. Then the hood was mounted, the fenders and the grille. The grille mount was adjusted until it was cosmetically correct by lifting the front of the tub which in turn allowed the front body mounts to fall into place. Now that the front and back where correct we made sure everything cleared in the middle, measured the rest of the body mounts and cut them. Now keep in mind we put no body lift on this, if you do, it can still be done using this method with a lot less hassle. Reinforcing strips are used at the mounting points of the body and fenders. This made for a very ridgid setup, you could actually lift at the grille and lift the front of the body if needed. I can remember going to shows and seeing Jeeps with no body lift with a very unsightly gap at the rear crossmember or at the grille. If you start in the back this can be elliminated. Again I can't say enough about this Shell Valley body. Give them a call or check them out on the web. Shell Valley Classic Wheels, Inc.
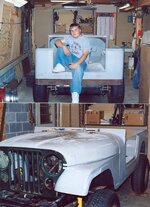
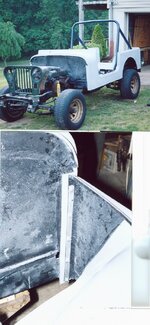
In this view you can see the difference that the shackle reversal made in moving the front axle ahead, centers the wheel a little better in the opening. Can't wait to get those 31's mounted on those factory chrome wagon wheels. Had to cut out for the taller wide track shock mounts, a saber saw made quick work of this. Start out by cutting only a little at a time. It's easier to remove than to add. We will probably add a rubber shield to cover the outside of the shock and mount to help cut down dirt from entering into the engine bay.
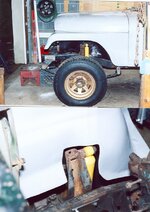
August 2006
Jeffrey wanted some kind of hood scoop for the CJ and we had looked at some "Bulge Hoods" which all had a raised center section but it just took away from the classic design that he wanted to retain. So the search was on. We needed something that would be close to the shape of the center raised section of a stock hood and the 401 emblems had to fit on the sides (that was a must) . These emblems were puchased off Ebay from member "berg102" eBay Feedback Profile for berg102. These are really top quality metal (not plastic) hand painted U.S. made. The hood scoop came from CJ Pony out of Harrisburg, Pa. Ford Mustang Parts | Mustang Parts & Accessories | CJ Pony Parts. This is strickly a Ford Mustang store so we felt a little out of place, but the people could not have been nicer. They even went out to the dumpster for a piece of cardboard so we could scribe a footprint of the scoop so we could see before we bought it, if it would fit the hood. The hood scoop had to clear the Laredo stripes we planned for the Jeep. If we would use it with the opening towards the front it would interfear with the stripes. So Jeffrey decides "how about cowl induction"? So we turned it around with the opening in the back and everything should clear. We might order a stripe kit first to make sure. As you can see this thing comes with studs glassed in so installation should be a snap. Stay tuned for the installation.
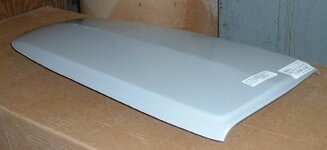
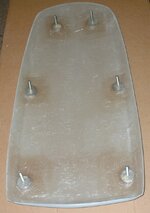
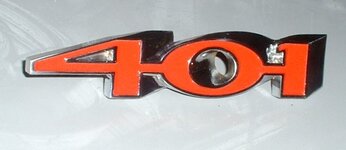