Exhaust manifold stud repair
Posi
Always Off-Roading Jeeper
- Posts
- 8,034
- Media
- 172
- Thanks
- 78
- Location
- New England
- Vehicle(s)
- 54 Willys 3B, FI 401, T-18, ARB Locked, Hinkey Sidewinder Winch
Broken exhaust manifold studs, most have experience with them some don’t. If mounted on the vehicle there are some temporary quick fixes like c-clamps (guilty), vise grips, u-bolts, or you can purchase ready made clamps some good some not so good.
Off the vehicle their really not hard to deal with I was lucky that I had at least one stud exposed.
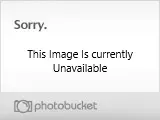
I soaked the threads with Kroil for a couple nights I also tapped on the stud to help the creeping process. I then welded a nut on the stud, used some heat and the stud backed out with ease. I filed the remaining broken stud flush then welded a flat washer on top (washer: same size hole as the stud or smaller). I then welded a nut on the washer and backed it out.
Side note: If the stud is broken off just below the surface you can use a ball peen hammer to dish the washer.
Other times I’ve had to drill out the stud and tap. Using this technique it’s important to find dead center on the stud and drill straight. I use a drill bit the same size as the stud (3/8”) to mark center then start with a smaller size bit 1/8” or less and work your way up to 5/16”. Use a 3/8’ 16 tap.
I don’t use extractors because they can break off in the stud and become time consuming extracting the extractor.
Mounting the manifold I use a light coating of mega copper on both sides of the gasket. I torqued the two inner bolts to 25 ft lbs and the four outer bolts to 15 ft lbs.
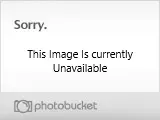
Hope this helps
Off the vehicle their really not hard to deal with I was lucky that I had at least one stud exposed.
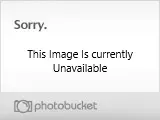
I soaked the threads with Kroil for a couple nights I also tapped on the stud to help the creeping process. I then welded a nut on the stud, used some heat and the stud backed out with ease. I filed the remaining broken stud flush then welded a flat washer on top (washer: same size hole as the stud or smaller). I then welded a nut on the washer and backed it out.
Side note: If the stud is broken off just below the surface you can use a ball peen hammer to dish the washer.
Other times I’ve had to drill out the stud and tap. Using this technique it’s important to find dead center on the stud and drill straight. I use a drill bit the same size as the stud (3/8”) to mark center then start with a smaller size bit 1/8” or less and work your way up to 5/16”. Use a 3/8’ 16 tap.
I don’t use extractors because they can break off in the stud and become time consuming extracting the extractor.
Mounting the manifold I use a light coating of mega copper on both sides of the gasket. I torqued the two inner bolts to 25 ft lbs and the four outer bolts to 15 ft lbs.
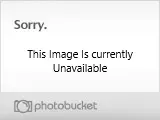
Hope this helps