Best engine and transmission placement? Cj7 engine swap 4.3 v6
76cj7chick
Old Time Jeeper
- Posts
- 1,235
- Solutions
- 1
- Thanks
- 8
- Location
- WA
- Vehicle(s)
- 1976 CJ7 Jeep with a engine/tranny/wiring harness out of a 1988 s10 blazer 4.3l v6 with th700r4 automatic tranny and a cj7 Dana 300 transfer case with Novak adapter.
Complete wiring harness from the s10 blazer. Painted with HOT PINK Pearl paint with standard sized metallic halographic pink flakes. Painted by me -a newb. New rear, front and side three wire LED lights, New parts, new custom dash-by me And a lot of guidance from fellow jeepers and lots of prayers etc.... :p
Hey everyone,
I'm just sending out this thread to get feedback on what is the best engine placement for my 4.3 swap into the CJ7 is.
Would love to hear from people who have swapped the 4.3 GM engine and th700r4 into their cj7s.
I installed the engine mounts however it looks like the engine sit still too high. However the only way to lower the engine anymore is to drill another hole back further in the frame but that would bring the entire drivetrain back.
Where the engine sits-my rear driveshaft is 20" long.
Also does the engine mount need to be straigh(as seen in the picture) or does it need to be tilted a little bit back?
Is it better to have the engine will further forward or is it better and the longer rear drive shaft or is it better to have a shorter drive rear drive shaft and push the engine for the back? Would I need to drill an additional hole in the frame to set the engine further back and lower or what is the best way because as it sits now it looks like the Transmission is too high and the angle from the Transfer Case to the rear axle might be a little too steep.
I'm just sending out this thread to get feedback on what is the best engine placement for my 4.3 swap into the CJ7 is.
Would love to hear from people who have swapped the 4.3 GM engine and th700r4 into their cj7s.
I installed the engine mounts however it looks like the engine sit still too high. However the only way to lower the engine anymore is to drill another hole back further in the frame but that would bring the entire drivetrain back.
Where the engine sits-my rear driveshaft is 20" long.
Also does the engine mount need to be straigh(as seen in the picture) or does it need to be tilted a little bit back?
Is it better to have the engine will further forward or is it better and the longer rear drive shaft or is it better to have a shorter drive rear drive shaft and push the engine for the back? Would I need to drill an additional hole in the frame to set the engine further back and lower or what is the best way because as it sits now it looks like the Transmission is too high and the angle from the Transfer Case to the rear axle might be a little too steep.
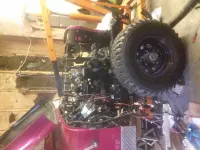
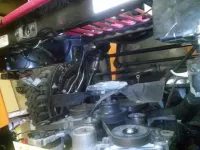

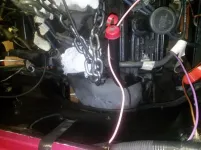
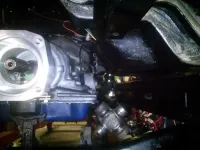
Last edited: