On Board Air
duffer
Active Jeeper
- Posts
- 480
- Media
- 9
- Thanks
- 45
- Location
- Bozeman, MT
- Vehicle(s)
- 1955 CJ3B: Dart/AFR aluminum 441 sbc, AGE M22W trans, "super" D18 w/ TeraLows & Warn OD, FF44 ARB/Dutchman Rear, D44 front-ARB/Reid/Dutchman, 4 wheel discs, York OBA, PP welder, 8274 w/ 9.5 XP motor/Zeon 12 contactor, glass/aluminum body, 33-12.5's;
1968 CJ5: all stock (V6/T86/D18/D27/D44) except 4bbl & headers and rear aux tank, HD rear 44 housing, Warn OD, Belleview winch, Whitco top (New Blue)
1968 CJ5: mostly stock (V6/T90/D18/D27/D44), unknown make 3" lift springs, 11" Bendix brakes, Warn OD, unknown electric winch, Kayline tire/jerry can carrier, Bestop Super Top (Old Blue)
1947 2A and 49 3A that may or may not get built, and several FC/wagon derelicts
A couple more thoughts on this.
IMO, the less restriction on the compressor inlet, the better. Just like any other piston engine. I modified the Solberg so it would sit directly on the modified Rotolock fitting.
Here is the assembled fitting-Rotolock on left and the air cleaner base sandwiches between the nut at the other end.
I also vented the crankcase with this assembly:
And finally, the tank drain. Initially I used a cable operated version, also from Grainger. That was a so-so affair. Burden Surplus Sales had a bunch of surplus diesel fuel shut off solenoid valves about that time and they work perfect. Just make sure to put some kind of filter on the outlet to keep debris out of it. A side benefit is you can scare the begeezus out of unsuspecting people at stop lights.
IMO, the less restriction on the compressor inlet, the better. Just like any other piston engine. I modified the Solberg so it would sit directly on the modified Rotolock fitting.
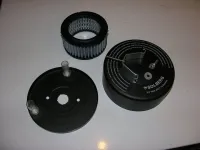
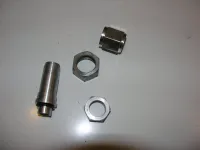
Here is the assembled fitting-Rotolock on left and the air cleaner base sandwiches between the nut at the other end.
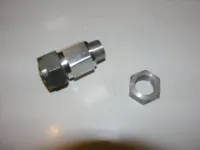
I also vented the crankcase with this assembly:
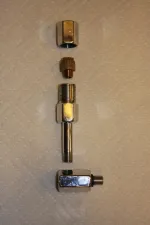
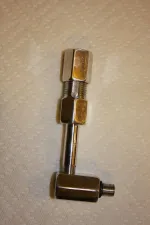
And finally, the tank drain. Initially I used a cable operated version, also from Grainger. That was a so-so affair. Burden Surplus Sales had a bunch of surplus diesel fuel shut off solenoid valves about that time and they work perfect. Just make sure to put some kind of filter on the outlet to keep debris out of it. A side benefit is you can scare the begeezus out of unsuspecting people at stop lights.