Doing a Ax15,and YJ Booster Swap
ThisGuyUKnow
Full Time Jeeper
- Posts
- 2,785
- Featured
- 2
- Thanks
- 1
- Location
- Harleysville, PA
- Vehicle(s)
- 1986 CJ7 Laredo 4.0,Nv3550,D300 Twin Stick,AMC20 3.31, 31 BFG
Honda vtx1800c
Got a longer bolt from lowes for that side that I couldn't get threaded. It was a tad too long so I got a nut and used it as a spacer and pressed it together. It popped back out a little but was enough to thread the original bolt. I was able to drop it down a little and tilt the engine enough to get in with extender and a joint for the socket driver and got the top two. One of the original starter bolts was way to short to make it through the metal in the new starter and still thread, so I had to run to the store and get a longer one.
For anyone doing this swap there are a few differences in the bolts between the 2 trannies. The bottom three bolts on the bottom of the T-5 bellhousing screw into the belhousing from the engine side of the Spacer plate. on the ax15 the bolt in the center at the bottom bolts the same way but is a different thread pattern and the two on the outside bottom both thread completely through and use a nut to bolt up. Luckily the bolts between the alignment dowels and the upper engine bolts on the T-5 bolt the same way so I used them on the bottom. The T-5 has a centered top bolt to the engine and the ax15 doesn't.
The bolts that were designed to mount into the housing were not the correct thread to take from the T-5 to the ax15. THey aren't structural and as far as i can tell they just keep the spacer plate from rattling so I left em out. If it rattles I will go to the pick and pull some other time.
I hooked up the starter. It came with my 01 nv3350 so i may be different if you get one from a donor, this one required I run wire from an acc on line to it.
I haven't got the Redline MTL in the mail yet so I didnt want to run the engine, also haven't fabbed a tranny mount yet but I did have the GF tap the starter while I stared at the output spline. It TURNS!!!! Eureka!!:cheers2: Hopefully by the time the AA clocking kit gets in I will have the tranny mounted and have figured out the hydraulic linkages.
Bolt I used to to press the BH onto the dowell
Just some shots I got trying to show the BH mated. You can see my 50 cent starter bolt.
For anyone doing this swap there are a few differences in the bolts between the 2 trannies. The bottom three bolts on the bottom of the T-5 bellhousing screw into the belhousing from the engine side of the Spacer plate. on the ax15 the bolt in the center at the bottom bolts the same way but is a different thread pattern and the two on the outside bottom both thread completely through and use a nut to bolt up. Luckily the bolts between the alignment dowels and the upper engine bolts on the T-5 bolt the same way so I used them on the bottom. The T-5 has a centered top bolt to the engine and the ax15 doesn't.
The bolts that were designed to mount into the housing were not the correct thread to take from the T-5 to the ax15. THey aren't structural and as far as i can tell they just keep the spacer plate from rattling so I left em out. If it rattles I will go to the pick and pull some other time.
I hooked up the starter. It came with my 01 nv3350 so i may be different if you get one from a donor, this one required I run wire from an acc on line to it.
I haven't got the Redline MTL in the mail yet so I didnt want to run the engine, also haven't fabbed a tranny mount yet but I did have the GF tap the starter while I stared at the output spline. It TURNS!!!! Eureka!!:cheers2: Hopefully by the time the AA clocking kit gets in I will have the tranny mounted and have figured out the hydraulic linkages.
Bolt I used to to press the BH onto the dowell
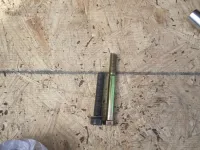
Just some shots I got trying to show the BH mated. You can see my 50 cent starter bolt.
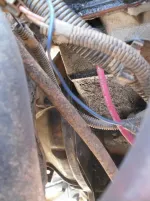
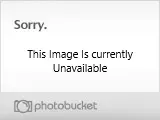
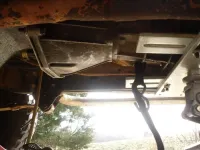