Build Thread The '80 FrankenJeep frame off reassembly
- Posts
- 7,316
- Media
- 5
- Solutions
- 1
- Thanks
- 157
- Location
- Roanoke, Va
- Vehicle(s)
- '80 CJ-7, AMC 304, T177, Dana 300, Widetrack axles (D30 & AMC20) w/ 3.73 gearing, MSD ignition,
Those are mine and have worked great for years and I didn't go to near the trouble you are.
Well, it's been one of those snowball things - I made a front bumper out of a chunk of structural channel, which required the tapering of the front couple inches of the frame rails to fit the taper of the back of the channel.
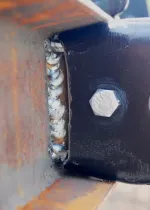
Then I decided to use the mounting brackets on the back of the bumper rather than upper and lower bolts..... Like the cleaner look. So now, after I posted the above question, I've been mulling this over. Worst case would be the bolts shearing thru the sides of the framing rail, pulling to the front, so I've cut a doubler plate to be welded to the outer side of the frame and another under the forward bolt for the hook. If it's overkill, at least it keeps me out of trouble, and allows more time for ugly welding......
Last edited by a moderator: